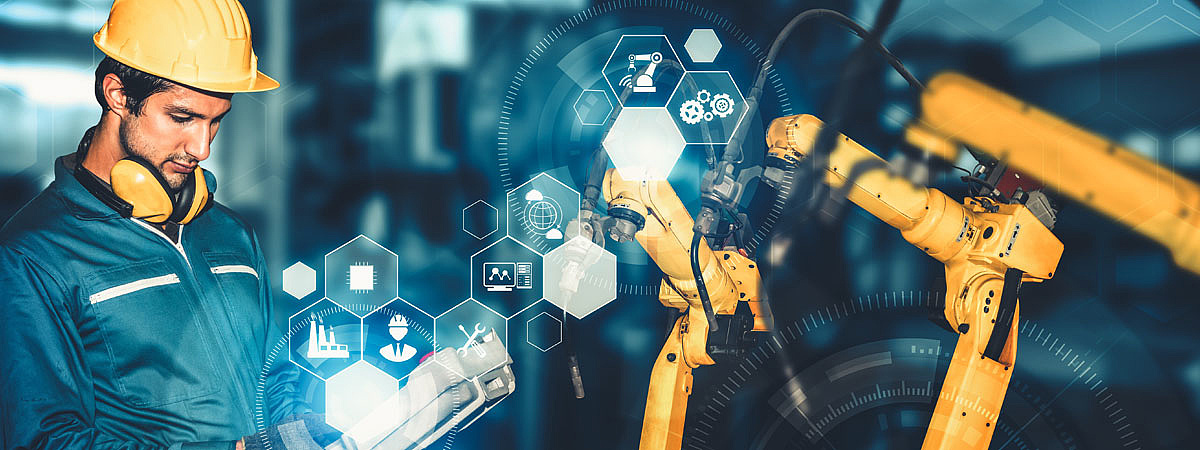
Successfully automating industry
OT systems? PLC? PCS? If these abbreviations mean nothing to you, then you are probably not a mechanical engineer. Don’t worry, neither am I! Nevertheless, we can talk about the role of OT systems in industrial automation. They are essential for safe and smooth production processes.
In short
- OT systems such as programmable logic controllers (PLCs) and process control systems (PCS) increase productivity, quality, and safety in manufacturing companies.
- They are used to control production processes, identify repair needs and find proactive solutions based on real-time data.
Industrial automation has made significant progress in recent years thanks to the use of OT (Operational Technology) systems. A memorable example of this is the introduction of industrial robots. Previously, machines and equipment were manually operated by workers, resulting in high labor costs, potential human errors, and life-threatening accidents. Now, with the help of robots, many manufacturing processes are already automated. But what do they encompass beyond that and what role do they play in industrial automation?
IT vs. OT
OT systems are a category of systems specifically designed for the automation of industrial processes and controlling physical processes. Examples of OT systems are programmable logic controllers (PLCs) and process control systems (PCS). In contrast, IT (Information Technology) systems focus on managing and analyzing information.
Safer and more efficient
The role of OT systems in industrial automation is diverse. However, one of their most important tasks is to control production machines and systems by collecting and processing data in real time. OT systems can also help improve efficiency by optimizing production processes and increasing machine utilization. By closely controlling and monitoring the manufacturing process, they also improve product quality.
Avoid expensive outages – in real time
Another important role of OT systems in industrial automation is safety. OT systems help to identify and avoid potential hazards and risks. They are used to maintain and service equipment to increase service life and reduce the need for costly repairs. They also help ensure that machines and plants are operated safely and prevent accidents. Monitoring collected data in real time also helps companies identify potential problems and proactively find solutions.
Conclusion
OT systems play a crucial role in industrial automation. Their importance should not be underestimated: They are an important part of industrial automation and help companies control, optimize and improve their production processes. Whether you are a mechanical engineer, an OT specialist or an IT admin, staying informed about the latest technologies and developments is increasingly important.
Read more
The ingenious principle of Linux software management
- Tags:
- uem,
- bms,
- linux,
- managed software